编者按:2018年,中国汽车市场连续十年蝉联全球第一大市场,东风日产轩逸、五菱宏光、上汽大众朗逸、长城哈弗单一车型年销量突破45万辆,排名第5至第9的一汽丰田卡罗拉、宝骏510、一汽大众捷达、一汽大众速腾、上汽大众途观、上汽大众桑塔纳,年销量在30万辆至38万辆之间。排名第10到第22位、年销超过20万辆的车型中,仅有吉利博越、帝豪,传祺GS4,荣威RX5五款自主品牌车型,其余座次被一汽大众新宝来 、迈腾,东风本田思域、东风日产奇骏、上汽通用昂科威等车型占据。这是合资车企占据市场绝对主导地位的时代,在“消费升级”的引领下, 合资品牌A+级车、B级车、SUV成为最热销的车型品类。产销两旺的红火局面下,鲜有行业内外的目光,关注到了一家成立于 1993年,以奥拓、雨燕等级入门级精品小车敲开千家万户大门,助力轿车最早走入家庭的长安铃木,已经在激烈的市场竞争下开启了企业重整。在外资紧急撤离,长安汽车运作两年后,更名“重庆铃耀汽车有限公司”的老厂得以重生,并在热销车型UNI-Z系列和 X5Plus系列的拉动下,2024年实现产量交付16.62万辆。“老厂结硕果”,合资车企转型之路虽道阻且长,但是随着凭借老合资厂在制造工艺上的优势,叠加自主研发智能车型的竞争力,重庆铃耀大踏步地走出了自己的转型之路,以实际行动完成了一份高质量转型样本。
在顺应时代发展的1993年,长安铃木应运而生,为世纪新纪元交替前后的中国市场贡献了若干款高性价比、家喻户晓的精品小车。25年后,当时代再一次把问卷交到“长安铃木”人手中的时候,还是那群人、那骨子干劲儿,在外方紧急撤离的大背景下,长安集团运作筹备2年后,变更为长安集团 100%独资的重庆铃耀汽车有限公司(以下简称“重庆铃耀”)于2020年应运而生,对于铃耀人来说,时代关上了不再适合经济发展规律的合资模式之窗,但同时也打开了更加适应灵活市场需求的汽车自主发展的康庄大道。
时至今日,重庆铃耀的首个五年发展周期恰逢国家"十四五"规划深入实施阶段,与中国新能源汽车产业"换道超车"战略形成历史性交汇。企业深度融入制造强国、质量强国、数字中国建设大局,以"科技创新+数字赋能"双擎驱动,构建起具有行业示范价值的智能制造体系,覆盖6大过程、15个关键项、26个要点的全生命周期品控网络。
通过优化供应链管理、强化技术创新、深化风险预控,不仅成为长安汽车“北斗天枢”智能化战略的实践标杆,更为中国汽车自主自研产业迈向全球制造价值链高端提供了生动样本。2019年刚刚完成转型的重庆铃耀年产不足2万辆,在长安汽车自研车型UNI-Z系列和 X5Plus系列的强力拉动下,2024年猛进至16.6万台,5年增长超7.7倍,产能使用率达到92.2%,为“十四五”规划的汽车产业发展添上浓墨重彩的一笔。
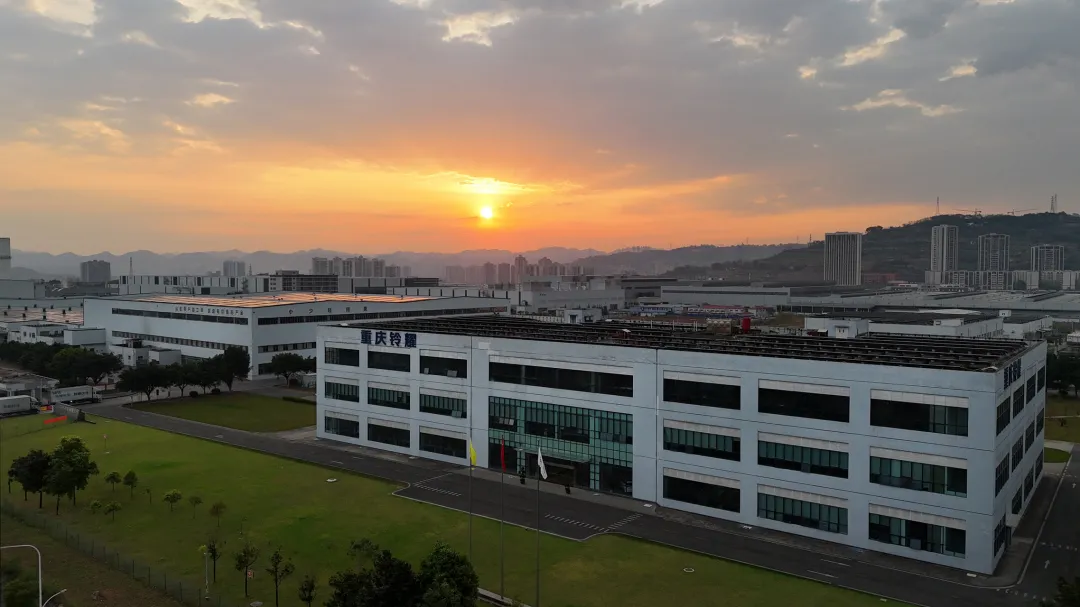
站在明亮的总装车间里,制造运营部周经理指着数字化看板告诉笔者:"我们保留了原有合资企业'改善无止境'的基因,现在又装上了中国制造的智能引擎。当被问及改制后的最大变化时,技术部高级经理杨考军从办公桌上拿起一本厚厚的《铃木品控手册》:“我们保留了国外企业'三现'(现场、现物、现时)的传统,不过把纸质表单全换成了云端系统,这样更加实时高效”,他打开手机展示CTQ管理平台,尺寸链验证、模具状态监控等数据实时跳动,“过去老师傅带徒弟要摸遍每个焊点,现在新人通过AR眼镜就能获得标准化指导。”
尽管铃木方从经营角度出发撤出了中国市场,但是长安铃木工厂已经储备了一套成熟的精益制造基因。这一优势,在为日后长安自主车型以品质和质量在市场上取胜奠定了基础,也回馈了合资时代留下的宝贵价值。
在冲压车间,每个工位都贴着醒目的5S管理标识。生产班长张师傅边擦拭设备边说:“合资公司精益生产留下的'整理、整顿、清洁、清扫、素养'规矩我们没有丢,现在设备更增加了自动报警功能,犹如给精益生产装上了飞翔的翅膀。记得在一次生产中,螺丝打紧设备异常导致力矩值不合格,全自动监控系统早于巡检员15分钟精准定位了生产异常,避免了批量返修。”这种传统与创新的融合,让重庆铃耀在2024年获得长安集团“标兵单位”称号。
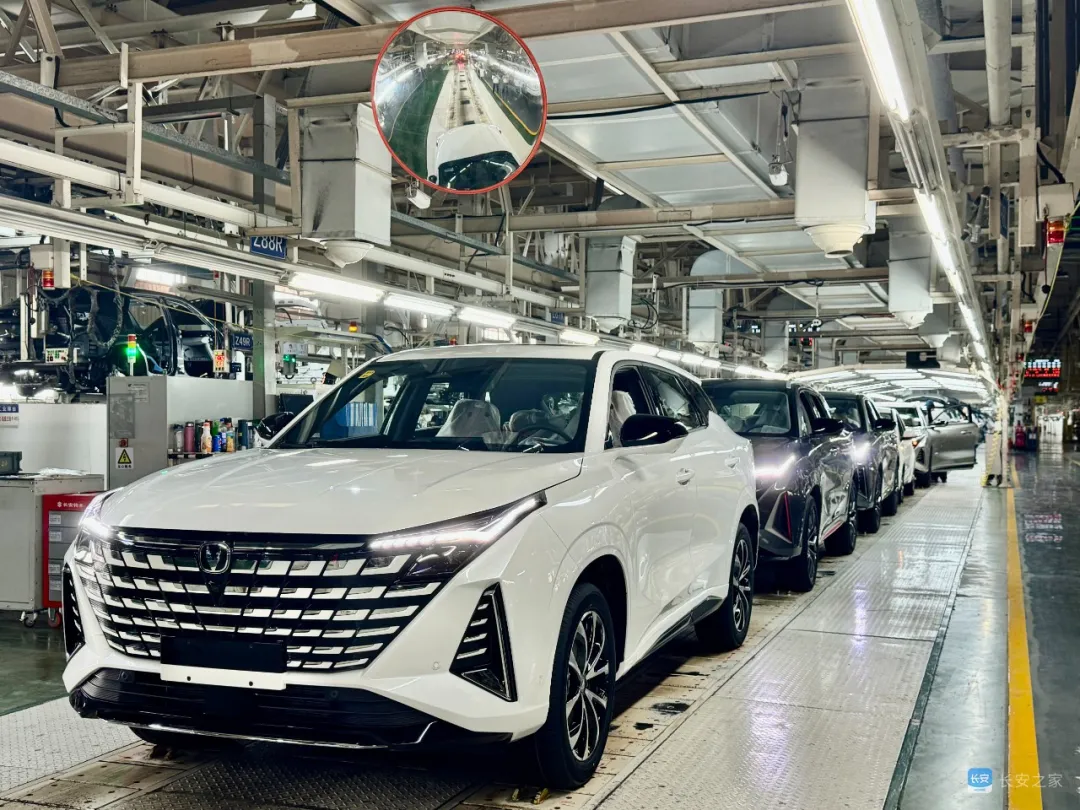
走访期间像这样的例子枚不胜举,让笔者能够深深地体验到在每一步制造工艺、每一个生产环节上,每位员工都充分利用原有合资的资源,发挥主观能动性进行升级改造,有效提高整体生产效能,促进公司整体向前发展,在新质生产力的赛道上给出了更加具象化的答卷。聚沙成塔,如果说车间里的点滴创新时转型过程中的“细胞级突破“,那么将这些突破系统化,继承化,规模化以实现效能最大化,则需要企业以更高的战略思维构建智能完整的制造体系。如下启示,也正是重庆铃耀响应国家产业升级号召的核心路径。
一、数字孪生驱动之智造升级:从车间的技术改良到企业级的战略重构,重庆铃耀用实践印证了一个真理:微观创新与宏观布局共振,才能形成最好的产业升级的内驱力。工厂经过18个月的探索与反复版本迭代,构建数字孪生体系,在虚拟世界的模型构建、布局规划,借助于仿真工具里数百种机器人型号及其运动轨迹数据对生产线运行进行仿真,大幅度提升了生产线设计准确率,从而有效地降低了过程中试错更改的成本,缩短了近50%的建设周期。重庆铃耀继续依托数字孪生技术,打造新车型验证平台,使新车型的验证效率提升95%。这一成就与《中国制造2025》提出的“推进信息化与工业化深度融合”战略高度契合。
二、构建“产学研用”协同的智能生态,核心技术自主可控是产业升级的根基。为此铃耀建立了“三位一体”的创新机制:
1、知识共享平台:深度融合长安汽车学习平台及外部资源,搭建“智能化软件培训体系”,通过线上课程与线下实训,将供应商的工艺经验与前沿的算法研究相结合,累计培养复合型STA工程师超30人,破解了传统制造业“软硬技术脱节”的痛点。
2、供应商共生模式:推行“现场跟线”制度,邀请核心供应商参与试制阶段的全流程管控。以某车载智能座舱项目为例,通过联合调试AR-HUD光学组件,将装配精度从±0.3mm提升至±0.1mm,故障率下降60%。
3、风险预控网络:基于历史车型数据库,构建“黑灰盒子边界尺寸预警系统”,针对新材料、新工艺等“六新“设立专项风险评估矩阵。在最新一代充电系统的开发中,该机制提前识别充电插座短路风险,通过系统尺寸链优化,将不良风险降低为0。
三、以供应链韧性赋能“双循环”新格局:面对欧盟碳关税、美国关税大棒,东南亚市场准入壁垒等挑战,重庆铃耀将供应链管理上升至战略高度,形成了自有的三大特点:
1、本地化协同:在某全球车型开发过程中,与泰国等长安海外基地复制“STA-供应商联合开发”模式,依托长安汽车全球五大研发中心,实现关键零部件的“区域研发、全球适配”。
2、动态韧性储备:建立“双芯供应商”清单,对芯片、动力电池电芯等战略资源实施“6个月滚动储备”。在”双芯“短缺危机中,该机制保障了某主力车型的产能稳定,2024年产值达历史新高。
3、绿色价值链:响应国家“双碳”目标,构建覆盖6万平方米的光伏发电系统,并联合供应商推行“绿电溯源认证”。在运行期内,发电量可达1.8亿度电,替代标准煤5.8万吨,减排二氧化碳18万吨,碳粉尘4.6万吨,二氧化硫约5.1千吨,减排氮氧化物2.58千吨,每年节省电费150万余元。
这是一条有迹可循的从“中国制造”到“中国智造”的跃迁之路。重庆铃耀的实践表明,中国汽车产业的竞争力正从“成本优势”转向“体系优势”。随着长安汽车“北斗天枢2.0”计划的推进,工厂将进一步深化AI大模型的应用,助力长安汽车实现2026年全场景L3级自动驾驶核心零部件自主配套的核心战略目标。
走访尾声,笔者一行人走在光伏板覆盖的厂房屋顶下,物流管理部同事又兴致勃勃地算起了"绿色账":“我们保留了合资公司供应商'同期生产'的配合度,又加入了中国速度,与27家核心供应商建立了数据直连,芯片库存周转天数从58天降到21天。”他指着正在装车的锂电池包说,“这就像极了我们的重庆火锅,老汤底不能丢,但涮的食材要常换常新,这样才能在新时代更好的满足南来北往食客,让大家多来重庆坐坐,又能常吃常新。”
在当下全球汽车产业百年大变局中,这座经历了从合资到完全自主演变的智能工厂将持续以精益为基、以数智为翼、以链群为脉,打好发展“组合拳”,不仅为长安汽车跻身世界前十车企注入强劲动能,更以中国智慧为汽车工业的可持续发展提供了崭新方案。(特约作者 土木)